
If you’ve ever baked a pizza, ironed a shirt, or dried your socks on a radiator, you’re more familiar with industrial heat than you think. Scale that up a few hundred times, and you’re in the world of factories and production lines, where heat powers everything from drying cereal to sterilising surgical equipment or making cement.
Yet, these essential processes come with a hidden cost: they are major contributors to CO2 emissions and thus to climate change.
Industrial Processes are essential, but come at a cost
Globally, industrial processes account for 30% (Figure 1) of total energy consumption and emit around 9 gigatonnes of CO2 annually (Figure 4) —roughly one-quarter of global CO2 emissions.
Figure 1: Share of total global energy consumption by sector (1990-2022)1
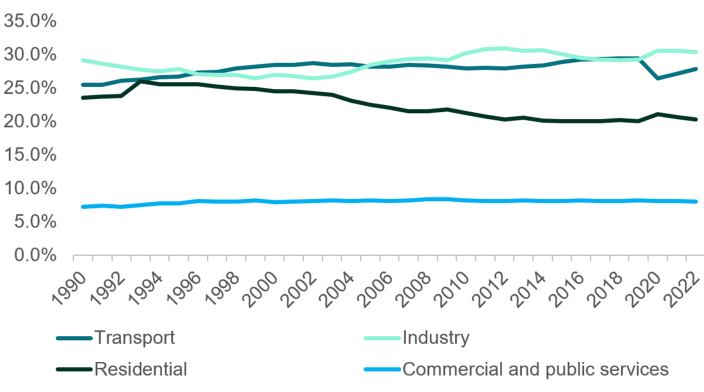
In Europe, heating alone represents two-thirds (66% ) [Figure 2] of industrial energy consumption, with nearly 80% (Figure 2) of that heat still generated from non-renewable sources.
Figure 2: Industrial energy consumption in the EU by application and source2
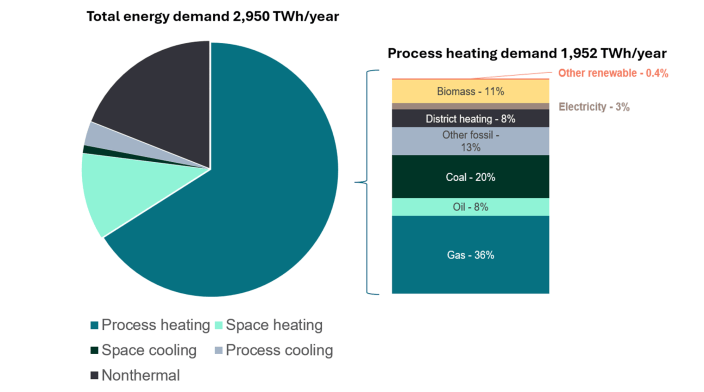
The issue boils down to the extreme temperatures required. Depending on the process, industries demand heat ranging from 100°C to >1,500°C. The higher the temperature, the harder it is to produce the required heat without burning fossil fuels. And that’s where the problem lies.
Industries that rely on high temperatures have operated the same way for decades. Switching to cleaner heat processes would require overhauling infrastructure and technology—an expensive and logistically challenging task.
The good news. Up to 60% of industrial heat demand could be electrified today with existing technologies. With continued innovation, this figure could reach 90% by 20354.
And the bad. As of 2020, only 3% of Europe’s industrial process heat had been electrified.
But, as the saying goes, "Where there’s a will, there’s a way." And the will is certainly there.
For example, in 2024 the EU revised its Industrial Emissions Directive (IED 2.0), implementing stricter rules on industrial emissions. The revised directive sets an overall emissions reduction target of 40% by 20503.
Solutions in Progress
Renewable energy solutions are steadily entering the industrial heat sector, especially for low- to medium-temperature applications (up to 600°C) in industries such as food and beverage, manufacturing, and paper & pulp4.
Figure 3: Industrial processes require a wide range of temperatures5
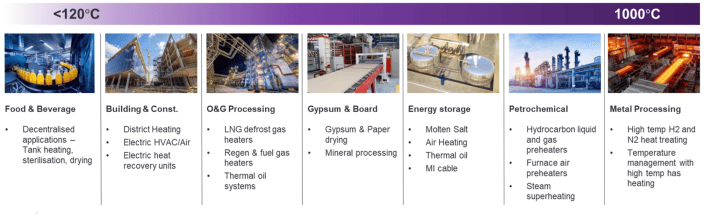
Technologies like electric boilers and heat pumps are becoming more mature and cost-competitive, enabling factories to transition without major disruption.
UK-based Spirax Group6, one of our portfolio companies, is at the forefront of industrial heat electrification.
Its TargetZero initiative focuses on electrifying industrial steam production methods with electric boilers and retrofit e-boilers, enabling cleaner energy transitions without major system changes. Paired with green electricity, this approach reduces Scope 1 and 2 emissions.
Alongside this, their PoweringZero initiative was launched for precise, energy-efficient heating up to 700°C, offering products like electric process heaters, heat trace or high-temperature heat pumps that recycle waste heat.
Tackling High-Temperature Processes
Cement, iron and steelmaking industries alone contribute over 50% (Figure 4) of global industrial carbon emissions annually. Their reliance on extreme temperatures (>1,000°C) makes decarbonisation particularly challenging, but there are examples of innovation.
Figure 4: Direct CO2 emissions by type of industry7
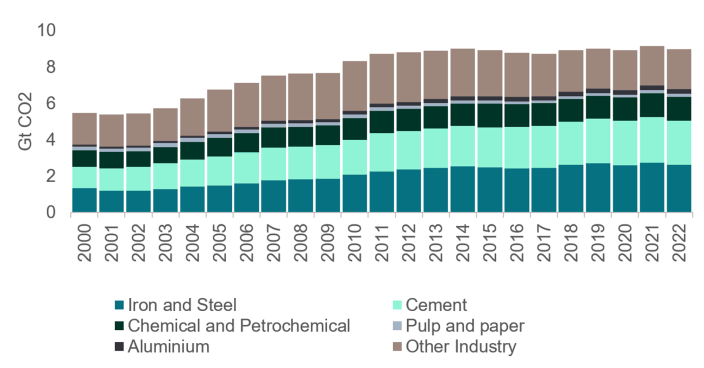
In iron and steelmaking, electric arc furnaces (EAFs) provide a cleaner alternative by using electricity to melt scrap iron or steel. While they achieve the >1000°C temperatures needed their energy demands are substantial, and if powered by non-renewable electricity carbon emissions will remain high.
Cement production presents an even tougher problem. Rotary kilns, used for calcination (a chemical reaction requiring extreme heat), are traditionally powered by burning fossil fuels. Electric kilns are feasible and show potential, but the technology is still too early for commercial use.
Collaboration in the chemicals industry was a notable 2024 success story. Linde, another WHEB portfolio company, partnered with chemical manufacturers BASF and SABIC to launch the first large-scale demonstration plant for electrically heated steam cracker furnaces. These are used in breaking down petrochemical compounds to smaller molecules like ethylene or hydrogen, which need to reach temperatures of up to 900°C. This breakthrough has the potential to reduce CO2 emissions by up to 90% compared to conventional methods8.
While challenges remain, such advancements highlight significant progress and offer promising solutions for decarbonising energy-intensive industries.
Turning Challenges into Opportunities
Industrial electrification faces both technological and economic challenges, with economic hurdles being a major barrier to adoption. The high upfront costs and downtime required to switch infrastructure can be discouraging for companies. In the long run, however, ongoing energy expenses have a much greater impact on total ownership costs. Unfortunately, in many regions, electricity costs more per unit of energy than fossil-based heat sources, despite being more efficient to use. This anomaly means that electricity-based heating can only be competitive where it is highly efficient – reducing the total amount of energy being used and offsetting the higher unit cost of electricity.9
It is for this reason that heat pumps are particularly attractive for low-to-medium temperature industries. Their ability to harness waste heat makes them highly efficient, lowering energy consumption and costs over time, even with higher electricity prices. When paired with thermal storage, companies can participate in demand response programs, further reducing energy expenses by shifting operations to low-demand periods.
For higher-temperature industries it’s not so simple, due to their substantial energy needs. Nevertheless, the uncertainty surrounding future carbon pricing and fossil fuel costs adds a compelling incentive for companies to transition sooner rather than later, to avoid potential financial and regulatory disadvantages.
Addressing these financial uncertainties will be critical to fostering wider adoption of electrification in industry.
Recent initiatives, such as the Regulatory Assistance Project’s 10-point plan10, propose strategies to accelerate progress. These include setting clear electrification targets, aligning high taxes and levies on electrification with fossil fuels, increasing funding for electrification projects, enhancing grid planning, and supporting research into industrial competitiveness under electrification.
Aligning economic policies with technological advancements can help industries overcome these barriers, making industrial electrification a practical and sustainable path forward.
Decarbonising industrial heat is one of the most significant challenges in achieving a net-zero future, but it is not insurmountable. With up to 90% of heat demand potentially electrifiable by 2035, the path forward is clear. Through targeted policies, technological innovation, and investment in electrification, industries will be enabled to transition to cleaner, more sustainable processes.
Sign up here to receive our monthly and quarterly commentaries in your inbox.
1International Energy Agency (2022) IEA Energy and Carbon Tracker 2022 (Figure 1)
2 De Boer, R., Marina, A., Zühlsdorf, B., Arpagaus C., Bantle, M., Wik, V., Elmegaard, B., Corberán, J., and Benson, J. (2020) Strengthening Industrial Heat Pump Innovation, Decarbonizing Industrial Heat (Figure 2)
3 https://environment.ec.europa.eu/news/revised-industrial-emissions-directive-comes-effect-2024-08-02_en?utm
4https://www.mckinsey.com/industries/industrials-and-electronics/our-insights/tackling-heat-electrification-to-decarbonize-industry
5 Spirax Group (2024) 2024 Capital Markets Day (Figure 3)
6 https://www.spiraxgroup.com/en
7 International Energy Agency (2023), Direct CO2 emissions from industry in the Net Zero Scenario, 2000-2030 (Figure 4)
8 https://www.linde-engineering.com/products-and-services/success-stories/2024/it-is-electrifying-steam-crackers-go-electric
9 https://www.chemistryworld.com/news/electrification-of-process-heat-stands-to-slash-industrys-emissions/4020003.article
10 Rosenow, J., Oxenaar, S., Pusceddu, E. (2024) Regulatory Assistance Project. Some like it hot: Moving industrial electrification from potential to practice